
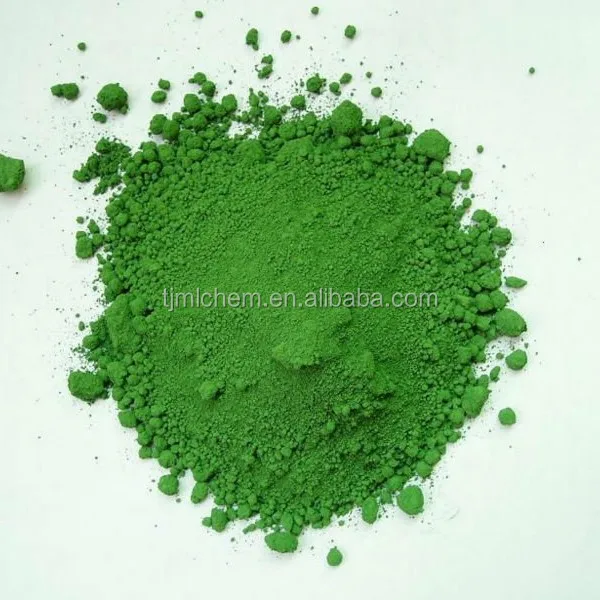
©️ 2023, The Economist Newspaper Limited.
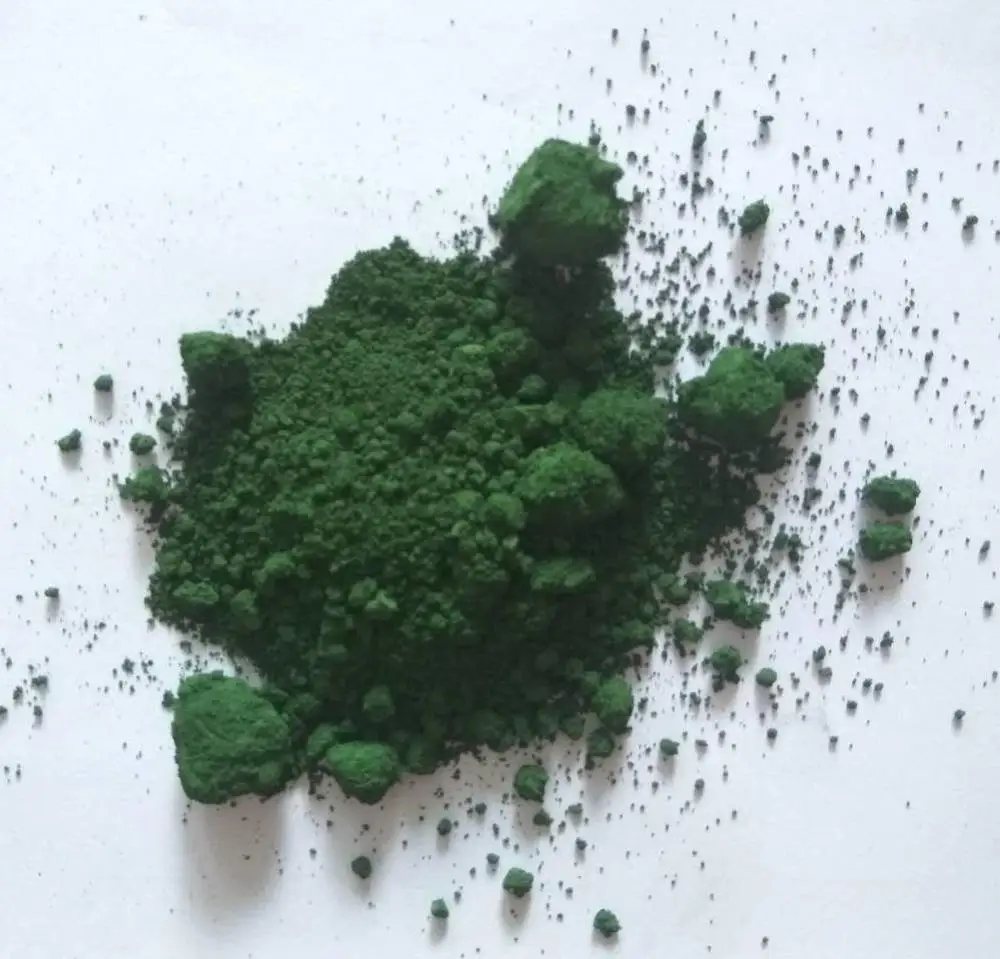
And complacency sometimes leaves the door open for truly disruptive new technologies. It also benefits from being a mere modification of an already familiar technology. Pure-hydrogen direct reduction does, it is true, have first-mover advantage in the race to green steel. (Iceland, with its low-cost hydroelectric and geothermal power, and location half way between North America and Europe, might find steelmakers queuing up.) Or those new plants could be built in places with cheap electricity. Legacy mills sited in coalfields in America and Europe might be replaced by plants next door to iron-ore mines, fed their electricity by connectors to the local grid. If the company’s process takes off, the geography of steelmaking could change radically. On May 30th the International Finance Corporation, an offshoot of the World Bank, said it had invested $20m in Boston Metal. It is in discussions with ArcelorMittal and Cleveland-Cliffs, two big steelmakers, about building its first test production facility, probably at an existing American steel plant. Working up from benchtop prototypes, Boston Metal now has a cell close to the size needed for commercial production. Mr Carneiro, who used to run CBMM, the world’s leading producer of niobium, reckons steel made this way could eventually compete on cost with the conventionally manufactured version, without needing the supporting bureaucracy of subsidies, tariffs and carbon taxes required for direct reduction by hydrogen. That makes electrolytic production modular and easy to scale up. To top things off, Boston Metal’s approach is based on cells that are much smaller than furnaces. This means the iron itself is chemically pure, and immediately ready to receive the various alloying elements used to produce steel.Īnother advantage of relying on electricity is that the world already produces and distributes plenty of it, whereas almost no infrastructure yet exists for making and supplying hydrogen. In Dr Sadoway’s process impurities are retained instead in the electrolyte. Sponge iron retains any impurities from the ore itself, meaning only high-grade ore can be employed for direct reduction. Boston Metal’s process produces liquid iron directly. Direct reduction produces “sponge iron", a solid that must be melted before being used to make steel. This arrangement has several advantages over direct reduction by hydrogen. Passing a current through the mixture both heats it, keeping it molten, and splits the iron oxide into its component elements. In this case it is a molten mixture of metal oxides, into which the iron ore is dissolved. The other electrode, the cathode, is the liquid metal itself.īetween these electrodes, as in any form of electrolysis, sits an electrolyte. Boston Metal employs, instead, anodes made of chromium, iron and a secret mix of other metals in an alloy that does not react with oxygen. But the process uses carbon electrodes, and the oxygen liberated at the anode reacts with this carbon to generate CO2. Instead of releasing CO2 or steam, its approach produces pure oxygen-which is not merely harmless, but actually valuable.Įlectrolytic separation of metals from their oxides is not new. Employing the insights of Donald Sadoway of the Massachusetts Institute of Technology, Boston Metal has created a way of separating iron from its ore by electrolysis. Mr Carneiro runs Boston Metal, a firm based not in Boston, but rather in Woburn, 17km to the north-west. But, thinks Tadeu Carneiro, not clever enough. The only by-product of such a reaction would be water (or rather, steam).Ĭlever. A widespread aspiration is thus to introduce direct reduction by hydrogen alone. As a consequence, steelmaking is reckoned responsible for about 9% of man-made greenhouse-gas emissions. Both create carbon dioxide, a greenhouse gas.
